Increasing the efficiency of chemical processes through the use of membranes
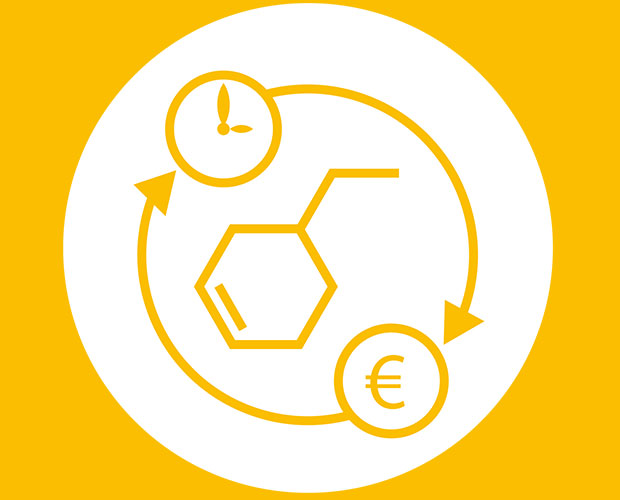
The key to increasing the efficiency of chemical processes is the use of membranes for product separation and product purification in downstream processing.
The driving force for membrane separation is not the temperature difference, but rather the gradient in the chemical or electrochemical potential, which, depending on the membrane process, is expressed as a gradient in pressure, partial pressure (or fugacity), electrical charge or substance concentration. Membrane processes are therefore significantly cheaper than thermal processes and, for example, use 80% less energy than distillation (Materials for Separation Technologies: Energy and Emission Reduction Opportunities, DOE report 4 May 2005).