Digital transformation in the chemical industry
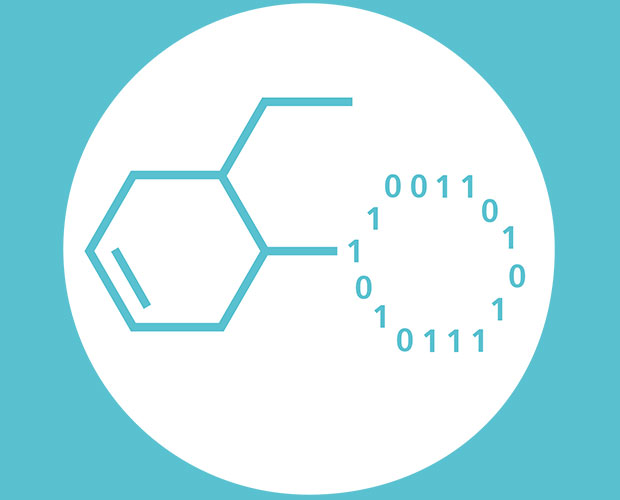
The Fraunhofer Chemistry Alliance has a high level of expertise in the modelling, simulation and optimization of chemical processes. Ontology-supported knowledge-based methods based on machine-readable expert know-how are combined with data-driven approaches to create reliable digital gray-box models of chemical production processes. On this basis, customized, interactive user interfaces provide a direct access to the knowledge graph and support well-founded decision-making by enabling the user to compare alternatives transparently, especially in the case of conflicting objectives. A user interface and its backend can be hosted both in a cloud and locally. Key components such as data storage and management are scalable and can be exchanged according to requirements.
Frameworks and platform-independent IT architectures from the Fraunhofer Chemistry Alliance can also link real measurement systems with virtual gray box models so that they can be viewed and evaluated together. In this way, applications for modelling, simulation and optimization of chemical processes can be integrated into their real-time monitoring and thus form the basis for innovative solutions for data-driven production planning and control. The alliance also offers access and development support for autonomous R&D laboratory modules, so-called Material Acceleration Platforms (MAPs) or Self-Driven Labs (SDL), which combine hardware automation, robotics and AI orchestration.
The success is remarkable. By using software tools from Fraunhofer, chemical companies have been able to reduce the energy consumption of processes worldwide by more than 10 %. Material acceleration platforms also have the potential to accelerate R&D processes by a factor of 5 - 10.
©AdobeStock / Fraunhofer ITWM